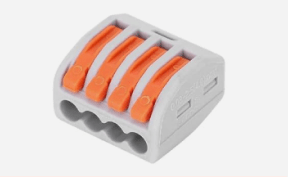
Are Push-In Wire Connectors Safe? What to Know to Use Them Safely
Push-in wire connectors are electrical components that simplify the process of connecting wires. They allow electricians and DIY enthusiasts to insert stripped wire ends directly into the connector, removing the need for screws or crimping tools.
These connectors hold the wire securely in place with internal metal clamps to ensure a reliable connection. They save time and reduce effort, making them popular in both new construction and renovation projects.
However, some may question the safety of push-in wire connectors, particularly concerning loose connections and their durability in heavy-duty applications.
We will discuss more about push-in wire connectors below and how you can handle them safely and effectively.
How Push-In Wire Connectors Work
Push-in wire connectors have an internal mechanism designed to hold wires securely and ensure proper electrical connections.
Inside the connector are metal clamps or spring-loaded contacts typically made from conductive materials like copper or stainless steel. These components are designed to grip the stripped wire end once inserted.
When the wire is pushed into the connector, the metal clamp inside automatically engages. The wire slides past a one-way mechanism that allows insertion but prevents withdrawal, giving you a secure hold.
The clamp exerts constant pressure on the wire, creating a tight, stable connection that remains intact even under vibration or movement. This pressure allows for good conductivity between the wire and connector, allowing electricity to flow without interruption.
The insulation on the wire stops at the edge of the connector, leaving only the bare copper wire in contact with the internal metal clamps. This also allows for minimal electrical resistance, promoting a safe and efficient connection.
The housing of the connector (which is usually made from non-conductive plastic) insulates and protects the connection from external factors like moisture, heat, or accidental contact.
This design simplifies the installation process by removing the need for screws or crimping, reducing installation time and minimizing possible errors.
When Should I Use Push-In Wire Connectors?
Push-in wire connectors are ideal for wiring projects where speed, ease of installation, and reliability are vital. They are most commonly used in applications like lighting fixtures, electrical outlets, switches, and small appliances.
These projects typically involve lower current loads and less mechanical stress, making push-in connectors a convenient option for quick, secure connections.
For lighting installations, push-in connectors save time by allowing multiple wires to be joined with ease. When it comes to outlets and switches, they offer a neat and organized way to connect wires without screws or crimping.
Push-in connectors are also commonly used in low-voltage systems like doorbells or thermostats.
However, push-in connectors may not be ideal for heavier-duty applications or environments prone to constant vibration or movement.
For example, they are not recommended for high-current loads like large appliances (like ovens or dryers) or heavy equipment. That is because the mechanical stresses could weaken the connection over time, leading to potential hazards.
In such cases, screw-on connectors or wire nuts may provide a more secure and durable connection.
Meanwhile, waterproof or specialized connectors may be better for projects exposed to moisture or extreme conditions.
Benefits of Push-In Wire Connectors
Push-in wire connectors offer many benefits when used correctly.
- Ease of Installation: Push-in wire connectors simplify the wiring process by letting users insert the wire directly into the connector, removing the need for screws or crimping tools. This saves time and effort, especially on large projects or when multiple connections are required.
- Time-Saving: The push-in mechanism significantly reduces the time needed to make electrical connections. Electricians can complete installations quickly, making these connectors ideal for tasks where speed is important, like residential wiring or retrofitting.
- Secure Connections: The internal metal clamps or spring-loaded contacts hold wires firmly in place for a reliable, stable connection. This reduces the risk of loose connections, which could lead to electrical faults or fire hazards.
- Compact Design: Push-in connectors have a streamlined, compact design, which helps organize wiring in tight spaces such as electrical boxes, lighting fixtures, and switches. These lead to cleaner and less cluttered installations.
- Versatility: Push-in connectors are suitable for various low—to medium-current applications, such as lighting, switches, outlets, and small appliances. This makes them a versatile tool for both professional electricians and DIY enthusiasts.
- Improved Safety: The plastic housing of push-in connectors provides insulation and protects the connection from accidental contact, reducing the chance of electrical shock or short circuits.
Potential Safety Concerns
If you are considering push-in wire connectors for a project, it is important to be aware of the potential safety concerns they can pose.
- Limited Current Capacity: Push-in wire connectors are generally designed for low—to medium-current applications. Because they can’t handle heavy electrical loads, using them in high-current circuits, such as for large appliances, could lead to overheating and potential fire hazards.
- Potential for Loose Connections: While the internal clamps provide a secure hold, improper insertion (such as not fully inserting the wire) or using incompatible wire sizes can lead to loose connections. Loose connections can cause arcing, increased resistance, and eventual overheating — all of which pose serious safety risks.
- Not Ideal for High-Vibration Areas: In environments prone to constant movement or vibration (such as industrial machinery or areas near motors), push-in connectors may become loose over time. This can compromise the integrity of the electrical connection, leading to failures or potential electrical shorts.
- Compatibility with Wire Types: Push-in connectors may not work well with certain wire types (such as stranded wire) unless they are specifically designed for it. Incorrect use can lead to poor connectivity, which can lead to overheating or electrical failures.
- Risk of Overcrowding Electrical Boxes: While compact, push-in connectors may still lead to overcrowding in electrical boxes if not properly managed. Overcrowding can increase the risk of overheating and make troubleshooting or future repairs more difficult.
Safety Standards and Certifications
Despite the potential safety concerns, push-in wire connectors must still meet certain regulatory standards and certifications to be considered safe. Below are some examples.
- UL (Underwriters Laboratories) Certification: Push-in wire connectors must meet UL standards (such as UL 486C) for safety, which ensures that they can handle rated voltages and currents. UL tests for factors like heat resistance, electrical conductivity, and durability under stress.
- CSA (Canadian Standards Association) Approval: In Canada, push-in connectors must be CSA certified, ensuring they meet Canadian electrical safety standards. CSA tests include evaluating the connector's performance under load and verifying its material safety.
- CE Marking (European Conformity): Push-in connectors need the CE marking for use in Europe, which certifies compliance with European safety, health, and environmental protection standards.
- IEC Standards (International Electrotechnical Commission): Compliance with IEC standards ensures that connectors are globally accepted and meet international safety benchmarks.
Push-in connectors undergo rigorous testing for heat, corrosion, vibration resistance, and overall reliability to ensure they meet safety and performance standards before being certified for use.
Push-In Wire Connectors vs Other Types of Wire Connectors
Push-in wire connectors might be confused with other types of connectors.
Below, we will make the different kinds of wire connectors more clear.
Push-In Wire Connectors
Push-in wire connectors are user-friendly since you only need to insert the stripped wire into the connector.
They are quick to install and ideal for light- to medium-duty applications like lighting fixtures, outlets, and switches. However, they may not be suitable for high-vibration areas or heavy-load appliances because of the potential risks of loosening.
Screw-On Wire Nuts
Screw-on wire nuts are highly versatile and widely used in both residential and commercial electrical work.
They offer a secure, strong connection through twisting wires together and screwing on the nut, making them reliable in a broad range of applications.
However, they can be more time-consuming to install and may require more effort to ensure a tight fit — especially for larger wire gauges.
Lever Connectors
Lever connectors have a flip-open mechanism and provide a highly secure yet reusable connection. They are ideal for applications requiring frequent wire disconnections or modifications.
Lever connectors are more expensive but offer superior convenience and reliability — especially in areas with heavy vibration or for professionals needing flexibility during installations.
Crimp Connectors
Crimp connectors need crimping tools to compress the connector around the wire. They also require more skill for proper installation.
However, their excellent durability allows them to be used primarily in high-vibration environments or for heavy-duty applications.
Common Myths About Push-In Wire Connectors
There may be some myths surrounding push-in wire connectors. We will talk more about them below.
- Less Secure Than Screw-On Connectors: A common myth is that push-in connectors are less secure than screw-on wire nuts. It is true that improper installation can lead to loose connections. However, push-in connectors provide a reliable, stable connection comparable to screw-on connectors when used correctly and with the appropriate wire gauge. After all, their internal clamps are designed to hold wires securely.
- Cannot Handle Heavy Electrical Loads: Another misconception is that push-in connectors cannot handle significant electrical loads. While they are suitable for light- to medium-duty applications, many push-in connectors are UL or CSA-certified for specific current and voltage ratings. As long as they are used within their rated capacity, they perform safely and effectively.
- Only for DIY Use: Push-in connectors are often considered a DIY tool. However, they are widely used by professionals in residential and light commercial applications thanks to their ease of installation and reliability.
Tips for Safely Using Push-In Wire Connectors
If you are eyeing these connectors for your next project, below are some tips on how to use push-in wire connectors safely.
- Ensure the Wire is Fully Seated: Always push the wire fully into the connector until it is firmly held by the internal clamp. Incomplete insertion can lead to loose connections, arcing, and overheating — which pose significant safety risks.
- Use the Correct Wire Gauge: Ensure the wire gauge matches the specifications on the connector. Using a wire that is too large or too small can result in poor connections, reducing the effectiveness of the clamp and increasing the risk of failure.
- Avoid Reusing Connectors: Push-in connectors are typically designed for a single use. Reusing them may compromise the internal mechanism, leading to weaker connections. As such, always use a new connector for each connection.
- Inspect Wires for Damage: Before inserting wires into the connector, check for any damage or fraying. Damaged wires can lead to poor conductivity and increase the chances of a dangerous situation.
- Choose the Right Connector for the Application: Use push-in connectors only for light- to medium-duty applications within their specified current and voltage ratings. Avoid using them in heavy-duty or high-vibration environments where other connector types may be better.
- Follow Manufacturer Instructions: Always follow the manufacturer’s guidelines for proper installation, including wire preparation, the maximum number of wires, and torque requirements, if applicable.
Key Takeaways on Are Push-In Wire Connectors Safe?
When used correctly, push-in wire connectors are a safe and efficient option for many electrical projects. Their ease of use, time-saving design, and secure internal clamps make them ideal for residential and light commercial applications.
However, like any electrical component, their safety depends on proper installation, adherence to manufacturer guidelines, and ensuring they are used only within their rated capacity.
While they may not be suitable for heavy-duty or high-vibration environments, push-in connectors provide reliable and long-lasting connections when used properly. This makes them a valuable tool for electricians and DIY enthusiasts alike.