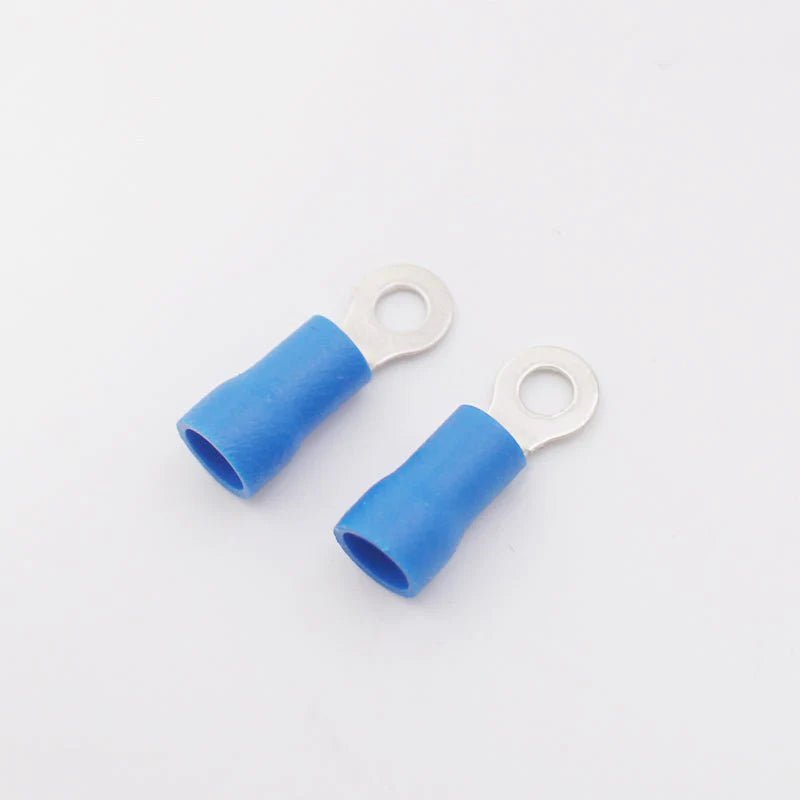
Eyelet Connectors: Understanding Their Role in Electrical Wiring
In the world of electrical wiring and connections, precision and reliability are paramount. One critical component that often goes unnoticed but plays a crucial role in ensuring the smooth operation of electrical circuits is the humble eyelet connector. These small, unassuming devices provide a secure and efficient means of joining wires and components, making them an indispensable part of any electrical system.
In this article, we'll delve into the world of eyelet connectors, their various types, applications, and the important role they play in electrical wiring.
What Are Eyelet Connectors?
Eyelet connectors, also known as ring wiring terminals or lug connectors, are small, cylindrical or ring-shaped metal components with a hole (eyelet) through which a bolt, screw, or stud can be inserted. The primary function of these connectors is to provide a reliable electrical connection between wires, cable applications, or other electrical components. They are typically made of materials like copper, brass, or aluminum, which are known for their excellent electrical conductivity and corrosion resistance.
Types of Eyelet Connectors
Eyelet connectors come in various sizes and designs to accommodate different wire connector gauges and applications. The key types of eyelet connectors include:
- Standard Eyelet Connectors: These are the most common type of ring eyelet connectors and are designed to be crimped or soldered onto the ends of wires. Standard eyelet connectors are available in a wide range of sizes to fit various wire diameters.
- Insulated Eyelet Connectors: To provide an additional layer of protection and prevent accidental electrical contact, insulated eyelet connectors have a layer of plastic or rubber insulation around the eyelet. This type is commonly used in situations where exposed metal might pose a safety hazard.
- Non-Insulated Eyelet Connectors: These connectors lack insulation and are ideal for applications where electrical insulation is not a primary concern. They are often used in industrial and automotive settings.
- Heavy-Duty Eyelet Connectors: Designed for high-current applications, heavy-duty eyelet connectors are typically larger and sturdier. They are commonly used in electrical systems with large loads, such as industrial machinery and transportation equipment.
Applications of Eyelet Connectors
Eyelet connectors find their applications in a wide range of industries and scenarios, including:
- Automotive Industry: Eyelet connectors are used extensively in vehicles for connecting wires to the battery, alternator, starter motor, and various other electrical components. Their reliability and ability to handle the high currents involved make them a staple in automotive electrical systems.
- Marine Industry: Due to their corrosion resistance and reliability in wet conditions, eyelet connectors are frequently used in marine applications, such as connecting electrical systems on boats and ships.
- Industrial Machinery: Heavy-duty eyelet connectors are essential for connecting power cables in industrial equipment like generators, transformers, and manufacturing machinery.
- Renewable Energy: Solar panels and wind turbines often use eyelet connectors to ensure reliable electrical connections in harsh environmental conditions.
- Electrical Panels: Inside electrical panels and distribution boards, eyelet connectors play a vital role in connecting wires to circuit breakers, fuses, and other critical components.
Installing An Eyelet Connector
Installing an eyelet connector is a relatively simple process that involves securing the connector to a wire or cable. Here are the steps to install an eyelet connector:
Prepare the Wire:
Strip the insulation from the end of the wire to expose the bare conductor. The length of the exposed conductor should be appropriate for the size of the eyelet connector. Refer to the manufacturer's guidelines for the recommended strip length.
Select the Correct Eyelet Connector:
Choose the eyelet connector that matches the wire gauge and type you are working with. The connector should snugly fit the stripped end of the wire.
Attach the Eyelet Connector:
For Non-Solderable Connectors:
Slide the eyelet connector onto the stripped end of the wire, ensuring that the wire fits snugly inside the eyelet. Then, use a crimping tool to crimp the metal barrel of the eyelet connector onto the wire. Make sure to apply even pressure to create a secure connection. The crimping tool should have specific dies or jaws for various connector sizes.
For Solderable Connectors:
Slide the eyelet connector onto the stripped end of the wire, ensuring that the wire fits snugly inside the eyelet. Heat your soldering iron to the appropriate temperature for your wire and connector type. It's typically around 300-400°C (572-752°F).
Apply solder to the wire and connector joint. The solder should melt and flow evenly around the joint, ensuring a strong connection.
Test the Connection:
After installing the eyelet connector, it's essential to test the connection for continuity and security. Use a multimeter or continuity tester to verify that there is a solid electrical connection without any breaks or loose components.
Properly installing eyelet connectors is crucial for the safe and reliable operation of electrical systems. If you have any doubts about your ability to install them correctly, it's advisable to seek guidance from a professional or consult the manufacturer's guidelines and recommendations for your specific connector and application.
The Importance of Proper Installation
While eyelet connectors are reliable components, their performance is contingent on proper installation. Inadequate crimping, faulty solder wire connector options, or insulation can lead to loose connections, overheating, or even electrical faults. Therefore, it is essential to follow manufacturer guidelines and best practices when working with eyelet connectors.
In conclusion, eyelet connectors are essential players in the world of electrical wiring, ensuring secure connections and the flow of electricity in various applications. Whether in the automotive industry, industrial settings, or renewable energy installations, these connectors perform a critical role in the reliability and safety of electrical systems.
Understanding their types and applications is crucial for professionals and enthusiasts working with electrical wiring to ensure that the current flows smoothly and that safe connectors can be optimized across the board.