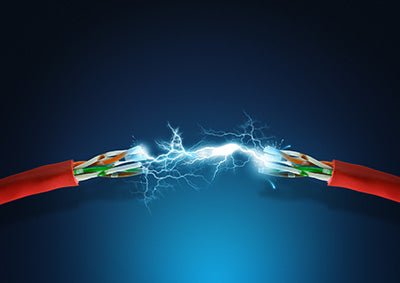
The Importance of Waterproofing Your Electrical Connections: How to Use Waterproof Solder Wire Connectors
Today, we use electrical connectors for just about everything. Just about everything we do has an electrical component to it, and connectors are important for ensuring that these components are placed properly within a system.
However, with waterproofing technology also being very prevalent, it has now been important for people to ensure that their connections are waterproofed and protected from the elements. Waterproofing electrical connections provides a great way to ensure that your system is resilient and able to operate regardless of the situation. This is especially true in environments and situations where exposure to water could pose a significant threat to the working connection you’re trying to build.
Generally, waterproof solder wire connectors stand out from other types of connectors in several critical ways. These include:
They’re built from PVC plastic, which is a generally more affordable material than most of its alternatives. And in many instances, it is easier to produce as well. So, for both producers and consumers, these connectors provide a cost benefit.
Waterproof connectors are also durable and rugged. They don’t get damaged so easily, unlike metal connectors which are made from different forms of metal coatings that can easily be damaged or chipped.
With waterproof connections, you get different Ingress Protection (IP) ratings. Some critical designations of these ratings can include submergibility, resistance to dust, and even protection from high levels of water pressure.
Finally, you can rest assured of an airtight connection.
Besides all of these, there are several standout features that you get from waterproof connections that their alternatives might not necessarily be able to provide. For instance, they come in different sizes, all depending on the number of cables that they can hold. So, you also get optimal flexibility on that end.
Â
Benefits of Waterproof Connectors
So, exactly how does waterproofing your electrical connections help you? We already pointed out several of the benefits you get from a waterproof connector and how these connectors tend to differ from alternative types of connectors. However, it is also worth looking deeper into some of the primary benefits that these connectors hold.
The first is the higher IP rating. With waterproof connectors holding higher ratings than most other connector types, you get to enjoy several benefits. For instance, most connectors tend to fall into the IP60-69 range. Depending on the specific rating, this means that they can fully protect your connection from high-pressure water jets, dust, immersion between 15 cm and 1m of water, and even long-term water submersion.
For instances such as use in marine applications and more, this is a very underrated benefit.
Â
How to Use Waterproof Solder Wire Connectors
Waterproof solder wire connectors are a type of electrical connector that is designed to protect wires from water and other elements. They are commonly used in outdoor and marine applications where wires may be exposed to moisture or salt water. Here's a step-by-step guide on how to use waterproof solder wire connectors:
- Strip the wire: First, you'll need to strip the insulation off the end of the wire to expose the bare copper. Use a wire stripper tool to strip about 1/4 inch of insulation from the end of the wire.
- Insert the wire: Next, insert the stripped end of the wire into the waterproof solder wire connector. Make sure the wire is inserted all the way into the connector and that it is centered in the opening. The connector should have two or three small metal tubes that the wire should be inserted into.
- Heat the connector: Use a heat source, such as a heat gun or lighter, to heat the connector. As the connector heats up, you will see the solder inside the connector start to melt and flow around the wire.
- Remove the heat source: Once the solder has melted and flowed around the wire, remove the heat source. Allow the connector to cool and the solder to solidify.
- Inspect the connection: Once the connector has cooled, inspect the connection to make sure it is secure. Give the wire a tug to make sure it doesn't come out of the connector. If it does, you'll need to reheat the connector and add more solder.
- Apply sealant: Once you're satisfied with the connection, apply a sealant to the opening of the connector to further protect it from moisture and other elements. Silicone sealant is a common choice for waterproofing wire connectors.
Â
And that's it! With these simple steps, you should be able to use waterproof solder wire connectors to protect your wires from the elements.
Â
FAQs
What is the best sealant for electrical connections?
Experts recommend using silicone sealant for your electrical connections.
How do you waterproof wire nuts?
To waterproof a wire nut, you need to start by choosing the right waterproofing material. You can use silicone sealant, electrical tape, or heat-shrink tubing. Apply the material to the nut and connection, then test it to ensure that the connection is strong and secure. From there, you’re good to go.
Should you put electrical tape around wire nuts?
While you can do this, it is also worth noting that it isn't overly necessary in some wire nuts.
How do you use weatherproof wire connectors?
Waterproof wire connectors can be used in any form of electrical system that will be required to operate close to a water body. However, they are also beneficial for their dust protection and more.Â
Â