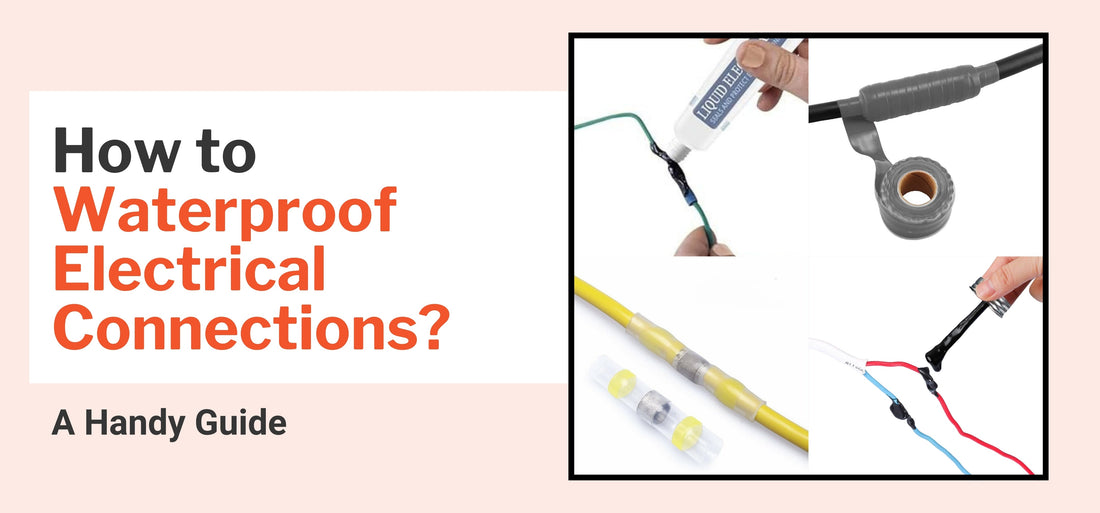
How to Waterproof Electrical Connections? A Handy Guide
Water and electricity do not mix. Moisture exposure can lead to short circuits, corrosion, damaged wires, and even fire hazards.
For this reason, protecting electrical connections from water is not optional—it is essential.
Waterproofing is critical in many applications. Outdoor lighting systems, automotive wiring, marine electronics, and garden equipment all face constant exposure to rain, humidity, or splashes. Without proper protection, these systems fail over time.
This guide explains how to waterproof electrical connections using effective and proven methods.
NOTE: For more insight into waterproofing your electrical connections, we also cover waterproof solder wire connectors in detail.
Understanding the Risks of Water Exposure
Moisture ingress in electrical systems causes more than just inconvenience. It can corrode metal contacts, weaken insulation, and create paths for electricity to arc, leading to shorts or total system failure.
Even a small amount of water can compromise exposed wires or unsealed connectors.
Common problems include flickering outdoor lights, dead vehicle circuits, or marine equipment that fails without warning. These issues can be prevented with proper waterproofing techniques and reliable materials.
Using secure options, such as T-tap connectors and other sealed connection methods, helps reduce risks. Protecting connections now increases equipment reliability, reduces maintenance, and supports long-term electrical safety.
Essential Safety Precautions Before Waterproofing
Before applying any waterproofing method, safety must be the top priority. Always disconnect power at the source to avoid electric shock or accidental short circuits. Confirm the system is de-energized using a voltage tester.
Wear personal protective equipment, including insulated gloves and eye protection, especially when working in damp or confined areas.
Before sealing, inspect all wires and connectors for signs of wear, corrosion, or exposed metal. Damaged components should be repaired or replaced immediately.
Applying waterproofing over already compromised materials will not provide lasting protection. For safer and more reliable sealing, use tested solutions, such as waterproof wire connectors, designed to withstand moisture and vibration.
Effective Methods to Waterproof Electrical Connections
There are several reliable methods for protecting electrical connections from moisture. Each one offers a distinct level of sealing, insulation, and durability, tailored to the specific application and environment.
Method 1 - Liquid Electrical Tape
Liquid electrical tape is a rubber-based compound used to coat and insulate exposed connections. It creates a flexible, water-resistant barrier that prevents moisture ingress.
Start by cleaning the connection to remove dirt, grease, or corrosion. Shake the can well before opening.
Use the built-in brush to apply a generous layer over the exposed area. Let it dry completely, usually within 10 to 15 minutes. For added protection, apply a second or third coat after the previous layer dries.
This method is ideal for hard-to-reach spots and irregular shapes. However, it may not be the best option for high-vibration areas or large cable bundles where more structural support is needed.
Method 2 - Self-Fusing Silicone Tape
Self-fusing silicone tape is a non-adhesive tape that bonds to itself when stretched and wrapped, creating a secure seal. It forms a durable, waterproof seal that leaves no residue.
To apply, stretch the tape as you wrap it tightly around the connection. Overlap each layer by about half its width for complete coverage. Continue wrapping until the connection is fully enclosed, then press the end firmly into place.
This method is particularly effective for temporary fixes, outdoor lighting, and vehicle wiring. It is flexible and handles movement well. However, it is best used on clean, dry surfaces.
For added sealing strength, combine with other protection methods where possible.
Method 3 - Adhesive-Lined Heat Shrink Tubing
Adhesive-lined heat shrink tubing offers dual protection. It insulates the connection while sealing out moisture with its internal adhesive lining.
Once heated, the tubing shrinks, and the melted adhesive fills gaps and bonds the tubing to the wire.
Select tubing with a diameter slightly larger than the diameter of the wire bundle. Slide the tubing over the connection. Use heat guns for soldering to evenly apply heat until the tubing shrinks and adhesive begins to flow. Let it cool and inspect for full coverage.
This method is ideal for outdoor applications, automotive repairs, and marine settings. It provides strong mechanical support and long-term waterproofing when applied correctly.
Method 4 - Silicone Sealant
Silicone sealant is commonly used in enclosures and junction boxes to prevent water from entering. It remains flexible after curing and resists environmental wear.
Before applying, thoroughly clean the surfaces to remove dust, oil, and old sealant. Apply a continuous bead of silicone around the opening or connection point.
Smooth the sealant using a gloved finger or tool and allow it to cure fully, which can take 24 to 48 hours, depending on the product.
This method works well for sealing cable entries, electrical boxes, and outdoor fixtures. It may not be suitable for small wire-to-wire connections. Avoid applying silicone on active circuits or over corroded terminals.
Method 5 - Waterproof Wire Connectors
Waterproof wire connectors are designed for fast, sealed electrical connections. They may include gel filling, rubber gaskets, or sealing caps. These connectors are also available in different sizes and configurations.
Start by stripping the wires to the recommended length. Insert them into the connector and twist or snap it closed according to the manufacturer's instructions. Select models with an IP67 rating or higher for use in outdoor or submerged environments.
Use wire nut kits, wire connectors, or butt connectors depending on your project. These products offer strong seals, reliable conductivity, and quick installation for both residential and industrial wiring needs.
Choosing the Right Waterproofing Method for Your Project
Selecting the right method depends on your environment, voltage level, and the degree of permanence required for the connection. Use this quick guide to choose effectively:
Adhesive-Lined Heat Shrink Tubing: Ideal for outdoor, marine, or automotive use due to its strong seal and dual insulation, although it requires a heat gun and is not reusable.
Self-Fusing Silicone Tape: Suitable for vehicle wiring and temporary outdoor fixes, offering flexibility and clean application. However, it may degrade over time and require a clean surface.
Liquid Electrical Tape: Works well in tight spaces and on irregular shapes thanks to its quick application, though it lacks mechanical strength and long-term durability.
Silicone Sealant: Ideal for sealing cable entries and junction boxes, as it provides a lasting barrier; however, it is not suitable for direct wire-to-wire applications.
Waterproof Wire Connectors: Reliable for residential, marine, and automotive setups due to their ease of use and fast, sealed installation, although sizing must be correct for a proper fit.
Ring Terminals with a Crimping Tool: Ideal for high-voltage or vibration-intensive systems, as they provide a secure and permanent bond, but require a wire crimping tool and ring terminals.
LED Connectors: Ideal for waterproof lighting applications due to their pre-sealed design and reliability, provided they are compatible with your lighting system and wiring layout.
Maintenance Tips for Waterproofed Connections
Waterproofing is not a one-time task. To ensure long-term protection, inspect all sealed electrical connections at least every six months, or more frequently in harsh environments such as coastal or industrial areas.
Look for signs of wear such as cracks in tubing, peeling tape, discoloration, or corrosion near the seal. Moisture inside enclosures, flickering lights, or inconsistent power can also signal failure.
When you notice damage or water ingress, replace or reapply the waterproofing method immediately.
Some materials, such as silicone tape or sealant, may require reapplication over time. Connectors in areas with constant vibration should also be checked for loosening.
High-vibration setups using wire eyelet connectors, fork connector kits, or spade connectors benefit from additional strain relief to prevent failure.
All in all, regular maintenance helps preserve the integrity of your electrical system and reduces costly replacements later.
Common Mistakes to Avoid
Improper waterproofing can lead to failure, even when using the right materials.
One of the most common mistakes is failing to clean the wires or surfaces before applying tape, sealant, or tubing. Dirt, grease, and corrosion weaken the seal, reducing adhesion.
Another issue is using incompatible products, like applying standard tape to high-heat areas or mixing materials that are not meant to bond. Always check for proper fit and material compatibility.
Lastly, neglecting to test the connection after sealing is also a frequent oversight. Use a continuity tester to confirm reliable contact.
Overall, just remember to follow the manufacturer's instructions for each product, whether using a copper cable lug or a push-in terminal block wire connector. Taking shortcuts often leads to early failure and costly rework.
Frequently Asked Questions (FAQs)
Here are quick answers to common questions about waterproofing electrical connections:
Can You Use Electrical Tape to Waterproof Connections?
Electrical tape is not fully waterproof and should not be relied on for long-term sealing.
It may resist light moisture for a short time, but it breaks down when exposed to water, heat, or sunlight. Over time, the adhesive can loosen, allowing moisture to enter the connection.
Is Heat Shrink Tubing Waterproof?
Adhesive-lined heat shrink tubing is waterproof when properly applied. The adhesive melts and seals the connection, blocking out water and debris. For best results, use a heat gun and allow the tubing to cool completely before handling.
What Is the Best Way to Waterproof Outdoor Electrical Connections?
The most effective method combines waterproof connectors with tapes or sealants specifically designed for outdoor use.
This layered approach protects against moisture, UV exposure, and physical stress. Always match the materials to the wire type and environment for lasting results.
Key Takeaways on How To Improve Electrical Connections
Waterproofing electrical connections is essential for long-term reliability and safety. Moisture can damage wires, cause shorts, and lead to system failure if left unaddressed.
Proactive sealing with the right materials prevents costly repairs and equipment downtime. Regularly inspect your connections and upgrade any areas exposed to water or outdoor conditions.
Choose methods that match your setup—whether it’s marine, automotive, or residential. Apply sealing products carefully and test for proper function afterward.
Explore our full range of waterproofing tools and accessories, including colored heat shrink tubing for easy identification and a piggyback space connector kit for multi-wire setups.
At SolderStick, we provide everything you need to protect your electrical systems with confidence.