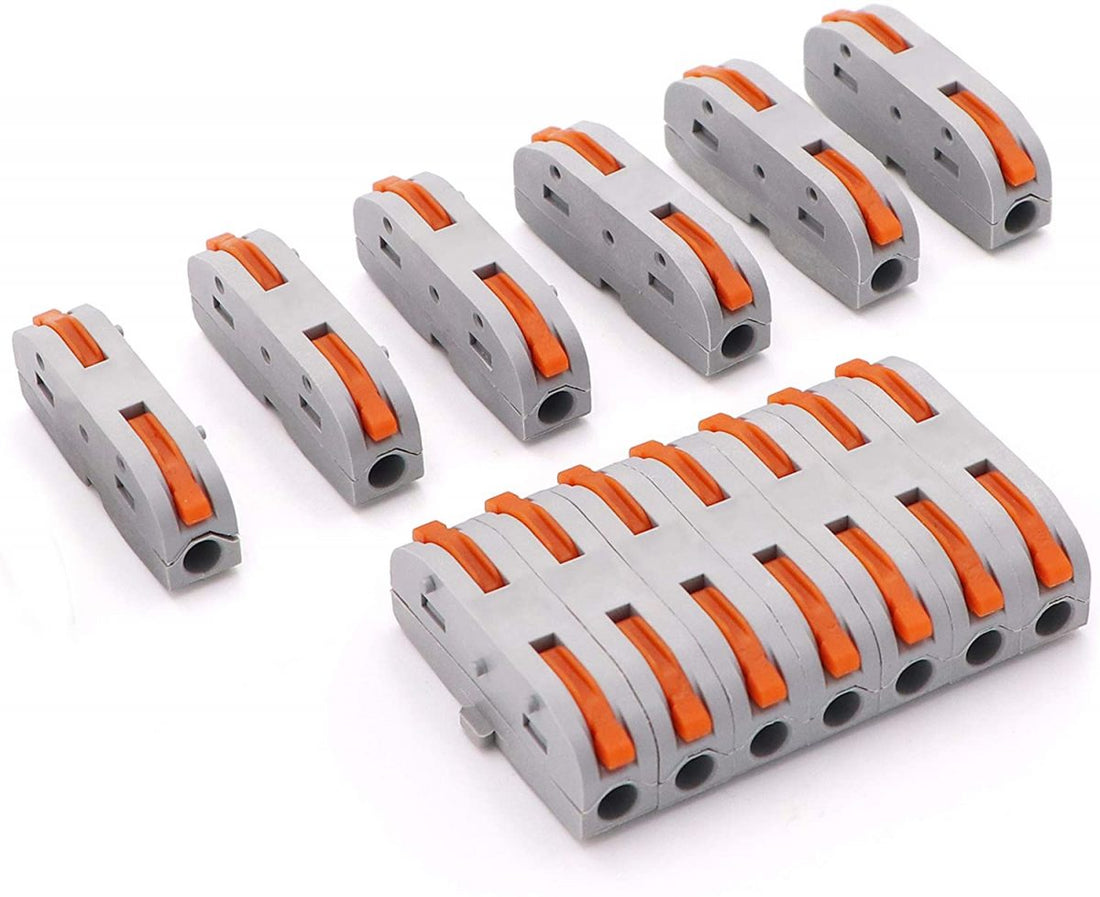
Splicing Connectors Demystified: Tips for Efficient Electrical Connections
Splicing connectors are the unsung heroes of electrical connections. These versatile components are used in a wide range of applications, from basic home wiring to complex industrial installations. Whether you're a seasoned electrician or a DIY enthusiast, mastering the art of splicing connectors is essential for safe and efficient electrical connections. In this article, we demystify splicing connectors and provide valuable tips to help you achieve seamless and reliable electrical connections.
What are Splicing Connectors?
Splicing connectors, also known as wire connectors or wire nuts, are devices used to join two or more electrical wires together. They come in various shapes and sizes, but their primary function is to secure wires, create electrical continuity, and insulate the connection to prevent short circuits or electrical hazards.
Types of Splicing Connectors
- Twist-On Wire Connectors: These are the most common type of splicing connectors. They consist of a plastic or thermoplastic shell with an internal thread that secures the wires by twisting them together.
- Push-In Wire Connectors: These connectors feature spring-loaded mechanisms that hold the wires in place when they are pushed into the connector. They are known for their convenience and ease of use.
- Crimp Connectors: Crimp connectors use a mechanical compression process to join wires, typically requiring a crimping tool. They are often used in automotive and industrial applications.
Efficient Electrical Connections with Splicing Connectors
Prepare the Wires:
Strip the wire ends to expose the conductive cores. Use a wire stripper or knife to remove the insulation while avoiding damage to the wire itself. Then, see to it that the stripped wire ends are clean and free from oxidation or corrosion. Use sandpaper or a wire brush if necessary.
IMPORTANT: Choose the Right Connector:
Select a splicing connector that matches the wire size and type. Most connectors are color-coded to indicate their compatibility with different wire gauges.
- Proper Twisting: For twist-on wire connectors, twist the exposed wire ends together in a clockwise direction. This twisting action ensures a secure and reliable connection.
Connector Installation:
For twist-on connectors, simply thread the connector onto the twisted wire ends until it's snug. Ensure that no bare wires are exposed. However, if you’re dealing with push-in connectors, insert the stripped wire ends into the connector until they are fully seated. The connector's spring mechanism will hold the wires in place.
Secure the Connection:
Give the connected wires a gentle tug to verify that the splice is secure. If the wires pull apart easily, recheck your connection.
Proper Insulation:
Apply electrical tape or heat shrink tubing to insulate the connection and prevent exposure to live wires. Ensure that there is no bare wire or conductor visible.
Label the Connection:
If you're working on complex wiring systems, label the connection with a tag or label to aid in future identification and maintenance.
Test the Connection:
Before restoring power or finalizing the installation, use a multimeter or a circuit tester to ensure that the connection is intact and functioning correctly.
Safety Considerations
Always ensure that the power is turned off before working with electrical connections to prevent electrical shocks or accidents. And, remember to follow all safety guidelines and electrical codes relevant to your location when working with electrical connections.
Conclusion
Splicing connectors are indispensable for making efficient and reliable electrical connections. By following these tips and taking safety precautions, you can master the art of using splicing connectors for a wide range of electrical applications, ensuring your projects are not only efficient but also safe and reliable. Splicing connectors may seem simple, but their proper use is key to the success of any electrical project.